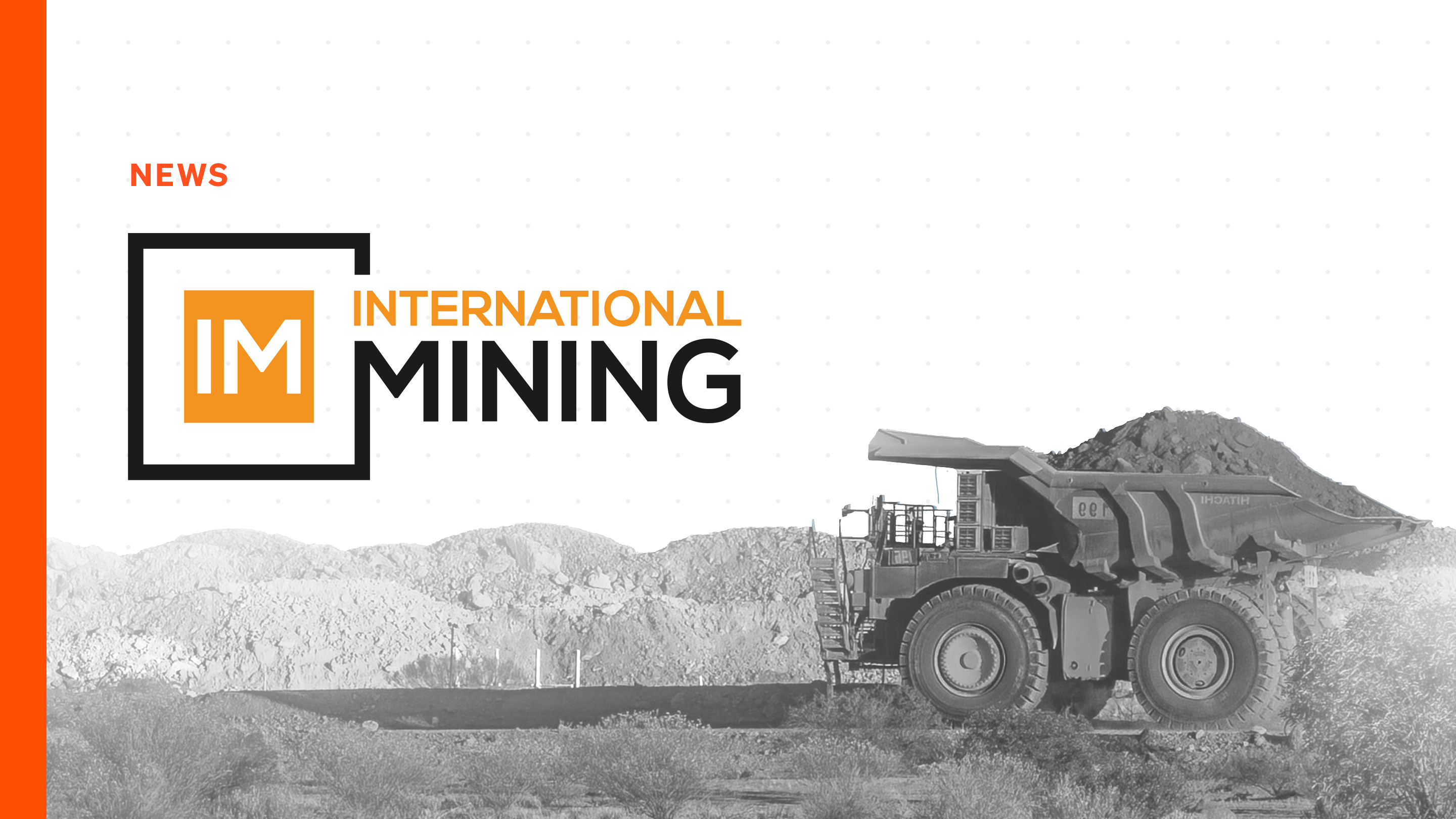
Automation Infiltration
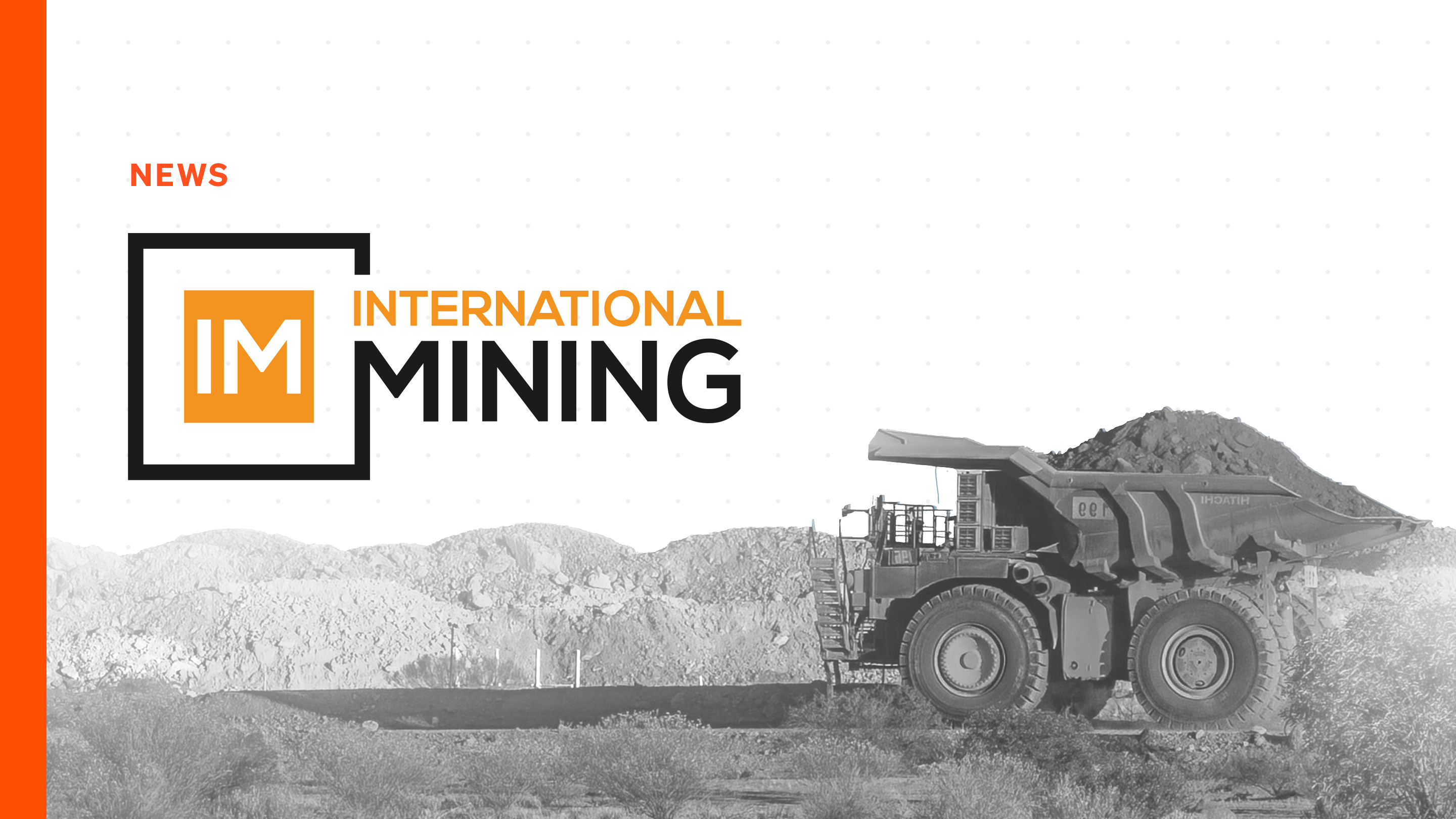
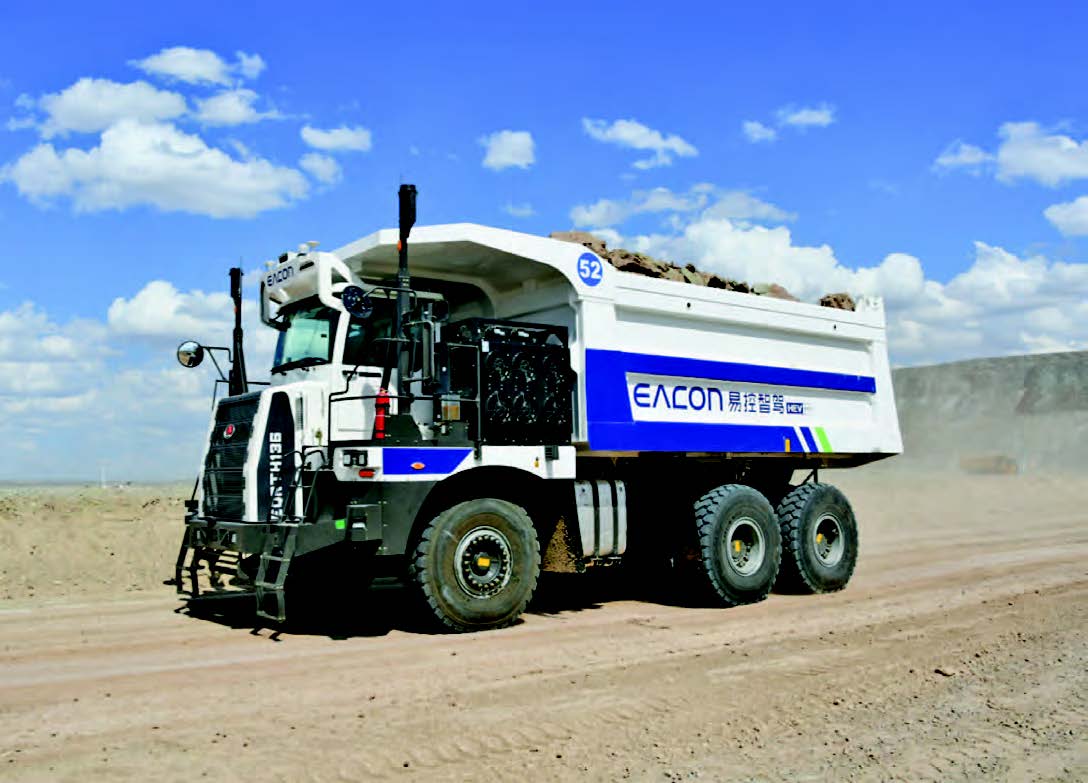
The new EACON136 running at the South Pit at the TBEA coal operation in China
When discussing the latest on automation technology, it is always good to reflect on how far things have come. Taking Caterpillar and surface mining truck haulage alone – the leading OEM now has almost 600 Command for hauling trucks running on customer sites. In more than 10 years in operation Caterpillar autonomous mining trucks have achieved 230+ million kilometres safely travelled and are running at 25 sites on three continents. More than 6.3 billion tonnes have been safely hauled by Cat autonomous trucks.
One of the most interesting recent rollouts was with leading global mining contractor, Thiess. On June 6, Thiess Group Executive Assets, Technical Services and Technology Ramesh Liyanage and General Manager Mining Vikesh Magan joined Pembroke Resources Chairman and CEO Barry Tudor, and senior executives from Caterpillar, Liebherr and Hastings Deering, to mark the commencement of mining at the Olive Downs Complex in Central Queensland.
The official moving of first dirt celebrated the safe mobilisation of Thiess people, plant and equipment to the complex, including a new Liebherr R 9800 excavator and several Caterpillar autonomous-ready 794 AC haul trucks. It represents a significant milestone for the Olive Downs Complex to deploy both Cat® MineStar Command for hauling and Command for drilling – Caterpillar’s autonomous hauling and drilling solutions.
Thiess, together with Pembroke, Caterpillar and Hastings Deering will provide 21 autonomous haul trucks, three autonomous drills and a private LTE network for the complex to enable full operations to commence in late 2023.
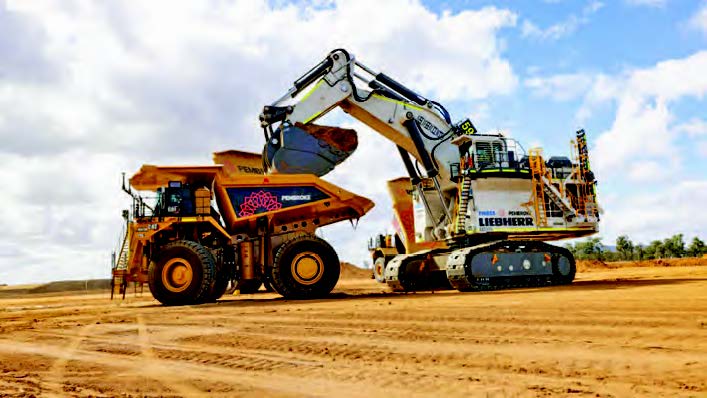
Autonomous Cat 794 AC, operated by contractor Thiess at the new Pembroke Resources Olive Downs coal operation.
Running LVs on the autonomous haulage system
Komatsu Ltd and Toyota Motor Corporation have launched a joint project to develop an Autonomous Light Vehicle (ALV) that will run on Komatsu’s FrontRunner Autonomous Haulage System (AHS). The partners stated: “To realise further safety and productivity improvements in mines by running autonomous haul trucks and automated ALV controlled by AHS, Komatsu and Toyota are launching an effort to jointly develop new technologies. Both companies are currently testing a concept ALV at their proving grounds, and plan to have a proof of concept at a customer site by around January 2024.”
Toyota adds: “Minerals and energy resources are essential in our lives and industries. Autonomy offers the opportunity to remove people from harm’s way and enhance safety. It can allow our mining customers the ability to continue the hard work of providing critical minerals despite the ongoing challenge of labour shortages in the mining industry. It can also provide additional safety measures to mine sites on which multiple pieces of equipment are operated, in an effort to reduce accidents due to human error.”
Since the launch of the world’s first commercial application of an AHS in 2008, Komatsu has established proven performance in various mine environments and has earned a reputation for safety and productivity. Currently, when AHS-enabled autonomous haul trucks and manual light vehicles used for maintenance or transport are running on haulage roads at the same time, autonomous haul trucks may decrease their speed or stop when passing light vehicles to avoid possible collisions caused by human error. On the other hand, customer demand for improved productivity in mine operations when it comes to autonomous haul truck operating efficiency remains an issue.
In light of those circumstances and in an effort to solve those issues quickly, Komatsu and Toyota have joined together to accelerate autonomy in mines. Komatsu will develop a new management program for ALVs on its AHS supervisory system, and Toyota will develop ALVs running automatically under AHS control.
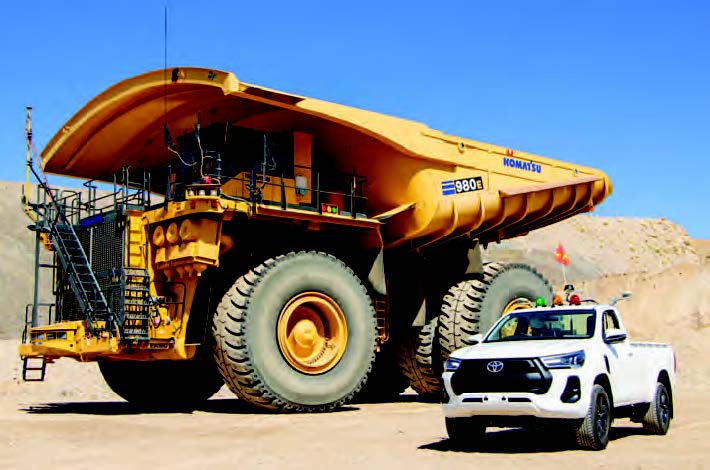
Komatsu Ltd and Toyota Motor Corporation have launched a joint project to develop an Autonomous Light Vehicle (ALV) that will run on Komatsu’s FrontRunner Autonomous Haulage System.
By operating Komatsu’s autonomous haul trucks and Toyota’s ALVs in mine sites utilising a common AHS, the companies say the following safety and productivity improvements will be realised across the mining operation:
- ALVs operating safely along haul roads
- Prevent accidental contact caused by driver, as may happen with existing manual light vehicles
- Minimise speed reductions or brief stops of autonomous haul trucks while passing light vehicles on a haul road
Toyota’s ALV autonomous operation will also accelerate further improvements and add functions that contribute to safety and productivity:
- Autonomous transfer of parts for other mining equipment working in the field
- Autonomous transfer of equipment operators for other machines such as loading equipment or bulldozers
Since Komatsu launched the world first commercial application of AHS in 2008, the company has deployed over 650 trucks at 22 sites in five countries as of May 2023.
The statement continued: “Komatsu AHS has earned a high reputation for safety and productivity from major global resource companies. Toyota makes safety a top priority and aims for zero casualties from traffic accidents as its ultimate goal. Toyota has been developing safe and automated driving technologies as part of its vision to provide ‘Mobility for All.’ In this development collaboration with Komatsu, Toyota’s automatic driving technologies will be utilised to contribute to the safety of people in their workplace.”
Komatsu adds that it will strive to create new values in order to take steady steps forward to the next stage for the workplace of the future and pass on a sustainable future to the next generation through the DANTOTSU Value. DANTOTSU Value is defined as customer value creation that generates a positive cycle of improvement of earnings and ESG resolutions in Komatsu’s mid-term management plan, entitled: ‘DANTOTSU Value – Together, to ‘The Next’ for sustainable growth.’
Komatsu and Toyota say they share a vision for developing an affluent and sustainable society to pass on the next generation. To do that, they say they are accelerating efforts to realise smart and clean future mine sites, leading to higher safety and productivity for their customers and partners.
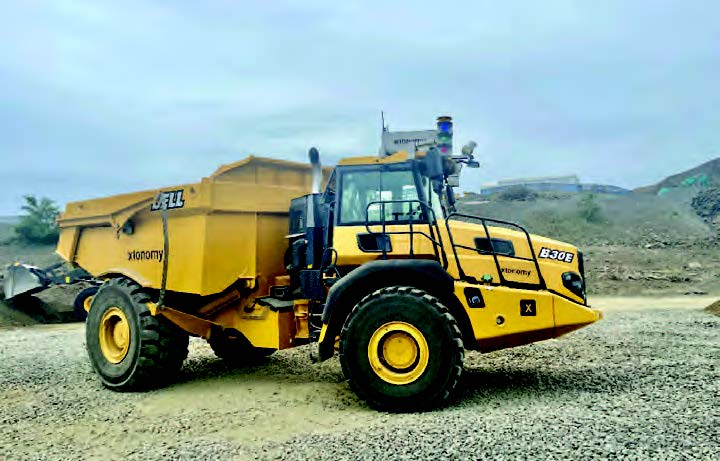
xtonomy recently held a live AHS demo on a Bell B30E at Steinexpo in Germany.
xtonomy live AHS demo at Steinexpo
xtonomy provides an advanced next-gen autonomous solution for mining and quarrying and argues: “xtonomy’s AI is the only commercially available system that is capable to navigate freely in unstructured and ever-changing environments such as in quarries. This enables autonomy for the first time also in complex dynamic sites and opens the technology to a wide range of customers.”
In a first for mining events, xtonomy demonstrated a fully operational AHS live in a quarrying show at this year’s Steinexpo 2023 in Germany, from August 23-26 in cooperation with Germany’s Bell distributor Kiesel GmbH on a Bell B30E 4x4. The event is held in Europe’s largest basalt quarry in Nieder-Ofleiden, which is operated by Mitteldeutsche Hartstein-Industrie AG. Visitors could observe how the machine operated in full autonomous cycles around the show grounds of the Quarry Vision area. The company told IM: “It was an eye-opener to the industry that AI can be leveraged today to solve the biggest industry challenges such as safety, labor shortage, OEE, cost and ESG factors.”
On the wider market, after many years of development xtonomy adds that its AHS for trucks is now transitioning to full production and is currently being rolled out to several applications. “The xtonomy AHS is designed for smaller truck fleets that may be fully orchestrated by the excavator or loader operator. Although the autonomous trucks automatically follow the excavator position on the bench and adapt queuing position, cusp point and loading position automatically, the operator may adapt all points to facilitate the process if needed.”
No additional personnel is required to supervise the fleet as all underlying processes are fully automated. The system uses robust radar onboard mapping and object detection to continuously perceive the environment and with motion planners that freely plan the best routes “and dynamically react to changes as opposed to driving from one fixed point to another on virtual rails.
“Furthermore, it handles the interaction of multiple trucks in such unstructured environments. This is only possible through a very high degree of autonomy at highest system levels. Several safety layers guarantee a safe operation with safe radio comms, high-precision GPS, radar and Ultra-Wideband (UWB) localisation. Manned machines may be integrated into the ecosystem for safe interaction in complex scenarios.”
Finally, xtonomy says its autonomy system does not require uninterrupted coverage of high-band-width comms throughout the mine-site which dramatically reduces the system implementation effort.
China’s EACON looks to go global
Established in 2018, China’s EACON describes itself a pioneering force in delivering field-proven solutions for autonomous haulage and zero-emission truck engineering in open-pit mines: “Our mission revolves around creating a secure, intelligent, and sustainable future for the mining industry.”
EACON has currently deployed over 150 autonomous trucks across two coal mines and a quarry. The earliest coal mine stripping project has been operational for more than three years, and as of June 2022, it has transitioned to 24/7 continuous operation without the need for safety drivers on board.
On July 18, EACON held a launch ceremony for the deployment of 100 hybrid autonomous mining trucks, the new EACON136. EACON took the lead in designing the core components of this vehicle model, which include a plug-in hybrid electric drive system, an intelligent vehicle-wide energy management system, a specialised range extender system for large-tonnage mining trucks, wire-controlled braking, and a fully hydraulic wire-controlled steering system. “These trucks can handle 90 t payloads, conquer 35% slopes, and reach 45 km/h. With 25 patented technologies, these trucks offer enhanced safety, efficiency, and reliability.”
EACON adds that its strategic partner, OEM LGMG, has been instrumental in truck production and the assembly of autonomous driving hardware. Recently, 102 new trucks have been successfully delivered, and autonomous driving testing has commenced at the mine site. EACON deployed these trucks at the South Pit of TBEA, China's highest-capacity coal mine, marking one of the largest fleets of autonomous mining trucks within a single mine worldwide.
With the maturation of autonomous driving technology, EACON has also embarked on expanding its overseas operations. The current focal markets include Australia, Chile, and the Middle East.
In June 2023, EACON established a subsidiary in Australia to support its endeavours in these regions. “Our expansion into Australia was motivated by its robust mining industry, favourable regulatory environment for autonomous driving, rich talent pools, and strong Sino-Australian trade relations.”
EACON Australia is currently engaging with potential partners to initiate pilot projects, offering two primary solutions for the Australian market. One is a comprehensive retrofit plan that transforms mainstream mining truck models into self-driving ones, regardless of the OEM and model.
The company adds: “Our truck engineering team, with over 30 talented individuals experienced in whole truck design and drive-by-wire solutions, has experience of successfully retrofitting more than 200 mining trucks, prioritising safety and reliability. The second solution is to provide factory-installed autonomous battery electric mining trucks. These trucks, while having a payload capacity of 60-90 t, can effectively meet the haulage needs of gold mines, lithium mines and quarries without increasing labour costs, making them viable replacements for existing diesel fleet.”
When it comes to the Chilean market, apart from the aforementioned two solutions, EACON is also closely considering the potential for introducing its hybrid truck model, the EACON136.
EACON’s aim it says is to bring field-proven autonomous system, refined over three years and across 150+ trucks in China, to global customers. “We strive to provide localised, tailored functions and features that benefit not only large-scale mines but also small and medium-sized operations. Furthermore, we are actively developing new energy-efficient trucks with larger payload capacities to meet diverse mining requirements.”
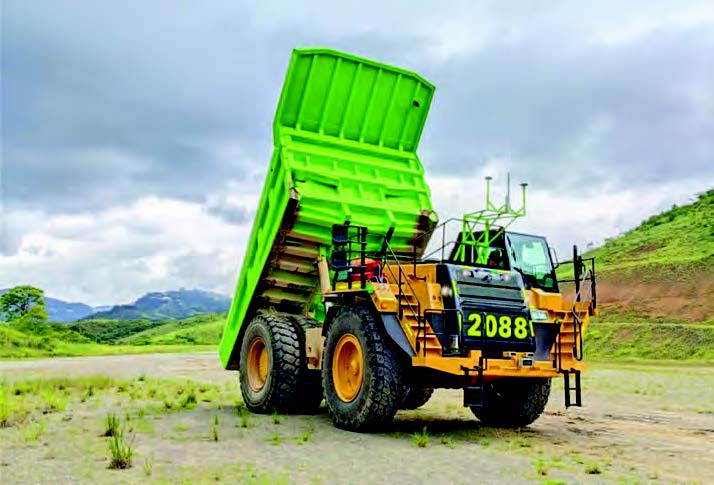
A combined Hexagon Mining and U&M driven OEM-agnostic AHS solution has begun trials at a mine in Brazil, as part of a plan to bring two AHS-enabled retrofitted Caterpillar 777 trucks to the operation.
EU&M and Hexagon ready to deploy AHS solution at Brazil mine
U&M Mineração e Construção S/A, as the largest native open-pit mining contractor in the Americas and one increasingly focused on sustainability, is about to embark on a major autonomous haulage project that could prove transformational for all sizes of mine sites across the globe.
The company has been busily working on an in-house Autonomous Haulage System (AHS) for several years, enlisting the help of Hexagon’s Mining division back in 2020 to ensure what it delivered to the market was a commercial proposition with widescale applicability.
Now the companies are ready to deploy their combined OEM-agnostic AHS solution at a mine in Brazil, which has already begun, as part of a plan to bring two AHS-enabled retrofitted Caterpillar 777 trucks to the operation. The first truck is already running, on trials, and all is going as planned. The second will be ready around October and U&M expects to have both on ‘commercial’ production by December.
The collaboration is seeing U&M carry out all mechanical changes to the 100-ton-class payload trucks to make them automation-ready without disturbing the OEM system. The contractor is also in charge of the navigation and the drive-bywire systems that the trucks will run on - the AutoNav and the AutoWire - or ‘autonomous driver’ as it could be termed.
Hexagon, for its part, provides the HxGN Autonomous Mining Mission Manager Solution to optimise the movement of autonomous and non-autonomous vehicles, and mine production activities through one interface; the World Perception solution to enable object detection, operator vehicle-to-vehicle and vehicle-to-person awareness; and some additional on-board infrastructure – such as sensors and an antenna.
This, according to the companies, makes for an autonomous contractor solution that can be rolled out anywhere in the world.
“The first project may involve Cat 777s, but what we are creating is a scalable platform that can be used on any truck,” Mauricio Casara, Commercial Director at U&M, told IM. “We are looking to improve on the legacy AHS solutions by making automation available to any size of mine with any type of trucks.”
As part of the company’s R&D work to this point, it has also retrofitted an autonomous solution on a Komatsu 730E, with that truck running at its proving grounds in Brazil.
Interestingly for this proof of concept involving the two Cat 777s, the plan is to enable the trucks to interact with both autonomous and manned vehicles in the haulage cycle from the off: an interaction that the traditional AHS providers have only just started to work on after more than a decade of industry deployments.
This is just one of the hurdles the solution will overcome, according to Andrew Crose, Vice President, Autonomous Mining, Hexagon’s Mining division.
“The world perception sensor stack that we have on board these machines will allow us to distinguish between trucks, light vehicles, berms, people and many other objects,” he said. “By leveraging this, we can ensure the trucks operate as safely as possible while being as productive as possible. That is key to achieving buy-in from all stakeholders involved.”
While the official partnership for this project was not signed until 2020, U&M has been utilising the GNSS positioning smarts of Hexagon – through the NovAtel business it acquired – for many more years.
This same GNSS solution is being leveraged in the two-strong autonomous truck trial along with V2X, 4D Radars, ultra-wideband time-of-flight systems and more.
Crose added: “It’s worth mentioning that around 60% of the autonomous machines running in the field have some Hexagon solution on them. We are sometimes providing the positioning, world perception, fleet and mission management, onboard autonomy and by-wire, all part of our interoperable strategy.”
While this initiative is inevitably going to pique the interest of those companies in charge of running these autonomous trucks, U&M has no plans to compete with the likes of Caterpillar and Komatsu when it comes to manufacturing automation-ready trucks.
“There are so many existing trucks out in the field that our clients are running; all of which can be retrofitted with the solution we are working on,” Casara said. “The whole industry talks about sustainability and how to mine sustainably, but the sustainable solution to achieving autonomous operations is not to build brand new trucks and equip them for automation; it is to retrofit the smarts onto them to enable that automation.
“This is the sustainable way to roll out the automation needed across the sector to achieve mining companies’ productivity and decarbonisation goals.”
FLANDERS ARDVARC Command Centre
Automation has long been the cornerstone of increased productivity and safety within mining settings. The FLANDERS ARDVARC Command Centre takes this further with its commitment to minimising operator interaction. It says: "By strategically reducing the need for human intervention, the Command Centre significantly curbs the potential for human error and associated safety risks. This progressive move is a testament to the latest technological advancements and a bold step towards ensuring a safer work environment.”
The FLANDERS ARDVARC Command Centre “brings a paradigm shift in the architecture of operator screens. With a meticulous focus on user experience, the Command Centre introduces a streamlined, intuitive interface that maximises the operator’s ability to oversee operations while minimising the necessity for direct engagement.” This transformation in the operator interface enhances efficiency and aligns seamlessly with the overarching safety goal of reducing personal interactions with machinery.
By fostering a system where machines communicate with each other to execute tasks, the Command Centre diminishes the risk of human exposure to potentially hazardous situations. This ensures that workers can oversee operations without directly being near the machinery, thus safeguarding their well-being.
The FLANDERS ARDVARC Command Centre also optimises the life of machines by effectively managing operations without the need for constant human supervision. By reducing wear and tear caused by frequent human interventions, the ARDVARC extends the operational lifespan of the equipment.
In remote locations where on-site human presence might be challenging, the Command Centre also thrives. Remotely managing operations and executing tasks ensures the same high standards of safety without requiring physical operator presence.
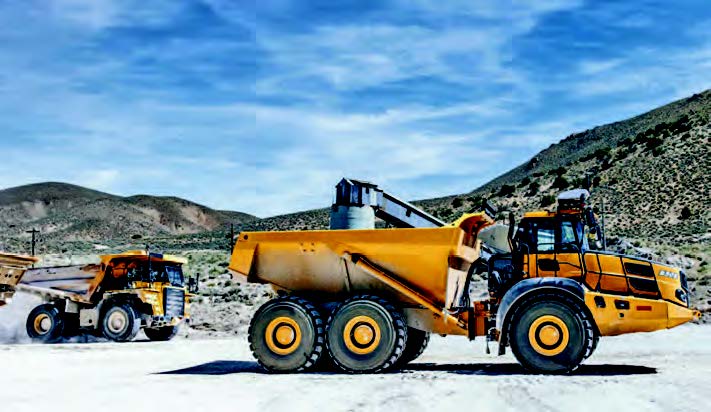
Whittle Consulting and Pronto say a new groundbreaking analysis demonstrates that when mining haul trucks are automated, bigger is no longer always better.
Pronto and Whittle study says bigger not better
Whittle Consulting, a global expert in integrated strategic planning for the mining industry, and Pronto, the Silicon Valley-based autonomy pioneer producing it says “the world’s leading Autonomous Haulage System,” have released a joint study titled: ‘Autonomous Swarm Haulage: The Economics of Autonomous Haulage with Small Trucks.’ The study, they say presents “a groundbreaking analysis demonstrating that when mining haul trucks are automated, bigger is no longer always better.”
Whittle Consulting modelled the net present value (NPV) of mining a representative copper orebody through four different scenarios, taking into account all facets of the mining value chain over an 18 year life-of-mine (LOM) horizon.
The modelled mine operating with a fleet of autonomous 40-ton haul trucks they say would realise a 31% greater NPV than if the mine were operated with a fleet of manually driven 100-ton off-road haul trucks. Autonomy significantly improved effective utilisation by reducing truck downtime, standby, and operating delays to 5% of availability versus 20% for manual vehicles.
One theorised flaw in the small truck logic was the prospect of traffic congestion caused by the increase in the number of trucks operating in the mine, potentially overcoming the efficiency gains of small truck and automation. In the study’s simulations, such traffic congestion did not materialise, according to Pronto and Whittle Consulting.
“The industry has long debated whether mining economics shift to favour smaller trucks when autonomous,” said Gerald Whittle, CEO, Whittle Consulting. “We’re excited to publish the first rigorous analysis that demonstrates that for most mines – the answer is yes.”
The study also concluded that converting an existing fleet of haul trucks to autonomous operations increased NPV irrespective of truck size. Both conclusions are consistent with industry experience and past studies, including Whittle Consulting’s 2018 Autonomous Haulage Report.
“This study is exciting because it clearly articulates one of the many ways in which autonomy is revolutionising the global economy today,” commented Anthony Levandowski, CEO of Pronto. “The results also illustrate why our strategy has been centred around making automation accessible to the majority of mines and quarries around the world that aren’t running the ultra class trucks that the legacy AHS providers have been focused on.”
Pronto had previously demonstrated the commercial benefits of an AHS capable of scaling down to the smallest trucks and smallest operations, and the Pronto-Whittle study it says substantiates that by identifying the specifics of why small trucks are favoured when autonomous: lower maintenance costs, better fuel efficiency, faster haul speeds, narrower benches/steeper pit walls are possible, and better overall fleet utilisation, among others.
On the choice of the 100 ton and 40 ton truck comparison, Pronto told IM that this was a realistic scenario where the same mine could have converted to smaller trucks (without major infrastructure changes) so it’s more of an apples to apples comparison. Pronto agrees there are lots of follow up studies that can and should be done including an ultra-class operation comparison, plus introducing electrification to the mix.
Wenco Open Autonomy installed on wheel loader at Rio’s Channar
At the Channar iron ore mine in the Pilbara, Rio Tinto continues to collaborate with partners, Scania and Wenco, to create an interoperable haulage solution for its autonomous haul trucks. The current project remains centred on what Rio Tinto calls a ‘Right Sized Autonomous Haulage System,’ part of its focus on new thinking on truck sizes in mining.
The work to date has been on Scania 8×4 XT 40 t class tipper trucks and a major part of the work has been looking at the issue of the sweet spot in truck size and class. Rio Tinto has stated: “Larger haul trucks, while already automated, consume more energy than current electricvehicle power sources can generate. By exploring truck size, we want to assess how big and small trucks can both be a part of the solution to reduce our emissions in the Pilbara and find fit-for- purpose solutions in mining.”
Ben Rogers, General Manager Services & Delivery Technology at Rio Tinto recently added in an online post on the project drivers: “Because we’ll have the flexibility to take the best autonomous haul truck offerings from our vendor partners to deliver the best outcomes in our operations. This includes accelerating the use of smaller, civil class electric trucks which will help to reduce our mining and operational footprints. This means narrower roads, a smaller mining pit and smaller mobile equipment maintenance infrastructure, creating less waste through the mining process and minimising our impact on the landscape and environment.”
He continued that it has successfully tested spot loading integration using Scania’s autonomous trucks with Wenco’s Open Autonomy system installed on a wheel loader and says it will continue to trial the joint solution over the next 12 months. Using Wenco’s software, the driver defines a loading bay, where the autonomous truck is sent to be loaded. Once the autonomous truck is full, it leaves the loading bay and carries on to the dumping point.
Wenco and parent company Hitachi are championing open standards including the implementation of ISO 23725 — the standard that decouples autonomous fleet control from OEM systems and enables customers to use existing haul trucks, FMS, machine guidance, hardware, network and other infrastructure already in place. The open systems platform provides the necessary FMS, spotting, mapping, traffic management, situational awareness, and controls to enable both traditional ultra class trucks and new entrants offering smaller or electrified trucks. Wenco is partnering with Oxbotica and other autonomy vendors to create Global Mining Group defined Level 5 autonomy for any ISO 23725 and open Drive-by-Wire standard supporting OEM vendor.
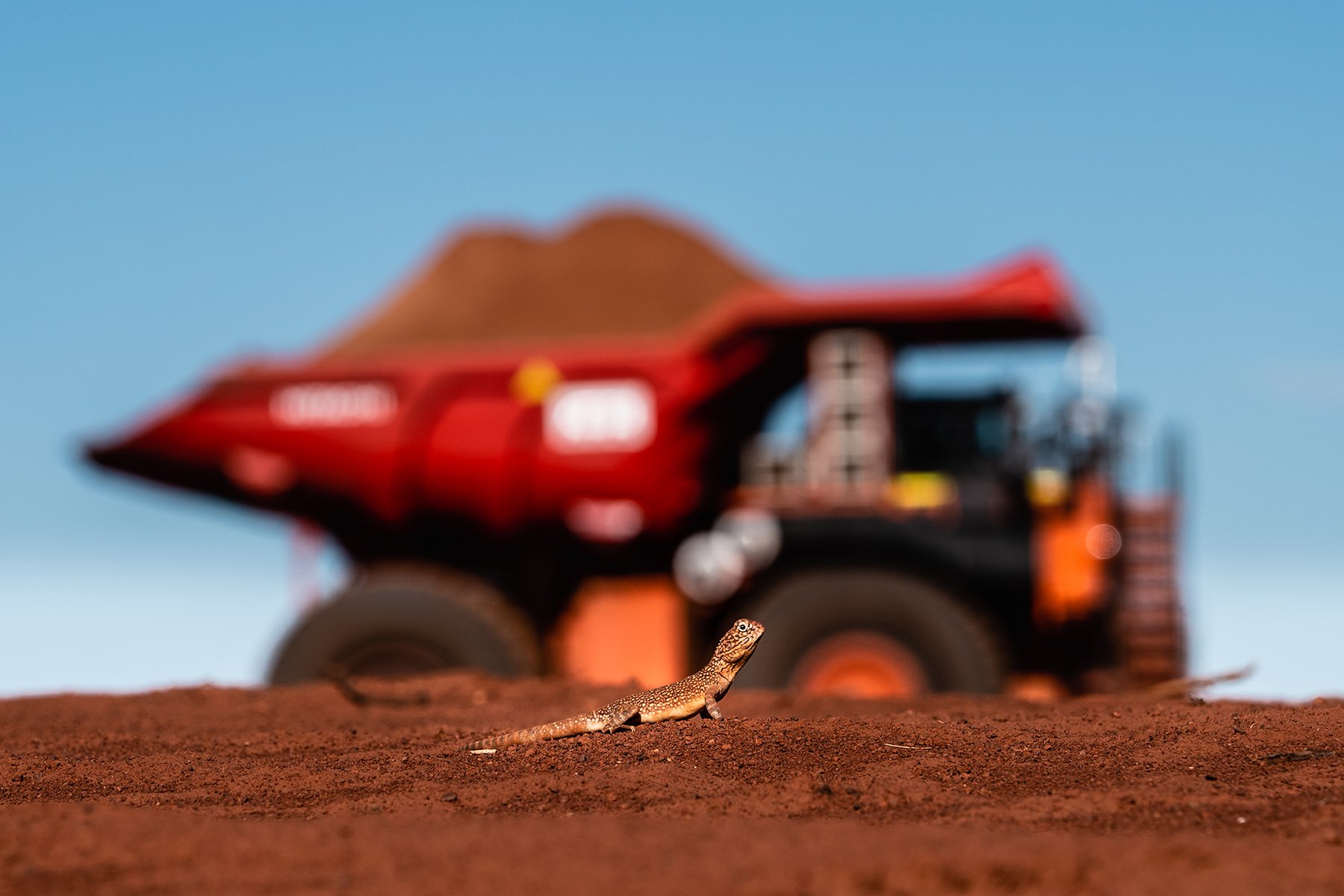
SafeAI says it has already hit some exciting milestones with Thiess-owned MACA in Australia.
SafeAI Autonomous Framework recognised for safety integrity
SafeAI, a relatively new global leader in autonomous solutions for heavy equipment, has announced what it says is a significant achievement for its SafeAI Autonomous Framework (SAF), which it also states is “the first operating system purpose-built for heavy industry.” SAF has been awarded the ASIL D certification, the highest safety integrity level in the industry.
SAF is described as a highly portable and reliable operating system for heavy industry, designed to simplify and accelerate the development and deployment of autonomous applications in embedded and real-time environments. “SAF gives mining and construction companies access to SafeAI’s certified and production-ready infrastructure to help them fast track their autonomous deployments and reap the benefits of self-driving equipment faster.”
Bibhrajit Halder, SafeAI Founder & CEO: “We are incredibly proud of this achievement, but we’re not stopping here...
We will continue to push the boundaries of what’s possible, driving efficiency, safety, and productivity in heavy industry operations. I want to extend my personal gratitude to our dedicated team, our partners, and our customers for their unwavering support and trust in SafeAI. This milestone is a testament to our collective efforts, and I’m excited about the transformative impact SAF will have on the heavy industry sector.Bibhrajit Halder SafeAI Founder & CEO
The certification further reinforces SafeAI’s rigorous commitment to safety. ASIL, or Automotive Safety Integrity Level, is a risk classification scheme defined by the ISO 26262 standard for the functional safety of automotive equipment. ASIL D is the highest level of this classification, indicating the most stringent safety measures to mitigate risks.
“SAF supports all safety-critical applications, ensuring the highest level of safety and reliability in SafeAI’s operations and those of its customers. The software API was developed in compliance with ISO 26262, IEC 61508, ISO 13849, and ISO 19014-4 as a software component and a Safety Element out of Context.”
The ASIL D certification of SAF “is further testament to SafeAI’s unwavering commitment to safety. This goes hand in hand with the company’s ‘Safety Above All’ value, and validates SafeAI’s efforts to create a highly reliable and safe operating system for heavy industry applications. This certification is not just an achievement for SafeAI, but a significant milestone for the entire heavy industry sector. It sets a new standard for safety and reliability, paving the way for broader adoption of autonomous technologies in heavy industry.”
SafeAI’s key projects with Obayashi and MACA are both progressing well. With Obayashi, it expects to be able to demo a retrofitted autonomous and electric Caterpillar 725 in Spain by the end of the year. “We’re extremely excited about the potential impact that the intersection of these two technologies can have. We’ve also hit some exciting milestones with MACA in Australia and are looking forward to being able to share some updates publicly soon.”
Also in relation to safety, the company just released the SafeAI Safety Report – a comprehensive overview of the safety protocols and workflow that it will use in the development and deployment of its autonomous vehicle technology. Bibhrajit had the following to say when SafeAI released the report: “When I named my startup almost six years ago, I wanted something that would reflect my vision for the company - with safety being at the core of it. This is the genesis of SafeAI — a deliberate dedication to establishing and adhering to safety protocols in the development of our autonomous technology solutions, as well as creating safe work environments in the challenging and diverse settings that we operate in around the globe.”
ASI adds more auto trucks at Roy Hill
ASI Mining, in conjunction with its distributor Epiroc, has received an order from Roy Hill Iron Ore to automate 18 Hitachi EH4000 haul trucks to be integrated with its current autonomous haulage fleet in Western Australia. The additional trucks will increase Roy Hill’s fleet to a total of 96 haul trucks which, once converted to autonomous operation, will make Roy Hill one of the largest single autonomous haulage system (AHS) sites in the world.
Once the entire fleet of 96 haul trucks is autonomous, it will boast not only being the largest AHS rigid fleet at a single site, but also the first site operating four different model variants from two different truck OEMs. The EH4000 fleet is being added to expand production capacity at Roy Hill’s mining operations. These new trucks will join an existing fleet of Caterpillar 793F (models SSP and CMD) and Hitachi EH5000 haul trucks, in the process of being converted to autonomous trucks at the site.
The AHS project at Roy Hill commenced its fleet expansion phase in January 2023, following completion of a two year validation period. It is anticipated all 96 of Roy Hill’s trucks will be fitted out by the end of 2024. ASI Mining’s Mobius AHS has been operating successfully 24/7 in a dedicated autonomous operating zone (AOZ) since July 2021, with Roy Hill achieving performance targets with a smaller fleet of 793Fs and EH5000 haul trucks.
“The receipt of this expansion order from Roy Hill signals their continued commitment to OEM agnostic autonomy and their continued trust in ASI Mining and Epiroc,” said Diederik Lugtigheid, President of ASI Mining.
Sandvik’s AutoLoad 2.0 & Flexible Safety Zone
Moving from surface to underground, and Sandvik Mining and Rock Solutions is introducing AutoMine® AutoLoad 2.0, a new AutoMine feature that enables fully automated production cycles for loaders operating in fixed drawpoint and dump point mining applications. This autonomous loading technology aims to increase loading cycle consistency while reducing equipment idle time and operating costs.
Building on its predecessor AutoLoad Assist, AutoMine® AutoLoad 2.0 features several design updates and significant improvements to enable operators to control multiple loaders with less intervention. The new feature allows operators to teach loaders different loading profiles for each drawpoint, eliminating the need for an operator to assist in the bucket loading procedure when mucking from drawpoints. These profiles may be saved for future use and default profiles are made available for several loader types.
“We have developed AutoMine® AutoLoad 2.0 to automate part of the production process that has been challenging for our customers,” said Jouni Koppanen, Product Line Manager Automation, Sandvik Mining and Rock Solutions. “AutoMine® AutoLoad 2.0 will allow customers to operate 24/7 without worrying about operator intervention during mucking once the profiles have been created. This new feature will help our customers see a direct improvement in their production and cycle time reliability.”
Extensive field tests with customers in Europe and North America have demonstrated that the new technology results in faster loading cycle times and consistent bucket fill factors, with an 8% increase in tons loaded per hour and 19% cycle time improvement.
“We are introducing new technologies and features to our existing platform to support our customers as they advance their AutoMine® operations,” said Ty Osborne, Acting Director Global Automation Product Line and Projects, Sandvik Mining and Rock Solutions. “We are confident that this development will enhance customer productivity by enabling fully autonomous production loader cycles while maintaining our industry-leading safety standards.”
Sandvik Mining and Rock Solutions is also introducing AutoMine® Flexible Safety Zone, a new feature for its AutoMine underground system for autonomous mining operations.
The new capability is, Sandvik says, designed to improve productivity and increase flexibility by enabling alternating safety zone states between autonomous and manual operation.
With the AutoMine Flexible Safety Zone, autonomous mining equipment can operate continuously in the automated area while allowing for intersections with manual equipment, according to the company. This capability makes it possible for manual equipment to cross automated equipment routes and share dump or load points. In addition, AutoMine access barriers are equipped with state-of-the-art technology that informs operators of the shared area status with visual and audible state indications, Sandvik explains.
Koppanen said: “Our new technology will increase the flexibility between manual and automated equipment by allowing manual operators to request access to a shared area. This request is designed to prevent automated equipment from entering the shared area while manual equipment occupies it. In addition, this flexibility will further enhance customer productivity and allow for continuous operation of both automated and manual equipment.”
Manual operators can request access to a shared area using a variety of actuators at the access barriers. Once acknowledged by the Supervisory AutoMine System and autonomous vehicles have cleared the area, access is granted and manual vehicles can enter safely. This procedure ensures the safety of all operators and equipment while allowing for more flexible setups, Sandvik says.
Elen Toodu, Director Global Product Line and Projects Automation, Sandvik Mining and Rock Solutions, said: “This new feature will enhance our customers’ AutoMine operations. We are giving operators the tools they need to adapt to changing conditions, which will ultimately improve productivity and safety in their mines.”
Epiroc’s Deep Automation step
For its part Epiroc has taken a major step with the launch of Deep Automation, which it describes as “the next step in automation solutions for underground material handling.” Deep Automation is Epiroc’s cutting-edge set of automation systems and applications, used to orchestrate loaders and trucks in underground mining operations. Developed with interoperability in mind, it says customers can take control of safety zones, production assignments and autonomous traffic in real time – boosting safety, consistency, and productivity.
Epiroc has a long history of developing and implementing automation solutions in mines all over the world. Deep Automation is the next step to create an even stronger automation offering with emphasis on interoperability, giving customers full control of a production area from the safety of a control room.
“We are very excited to offer the most interoperable automation solution on the market. This is made possible by a cross-platform interface between Deep Automation, mine planning tools, underground machines, and auxiliary equipment” says Gabriel Norefors, Director of Customer Solutions Material Handling at Epiroc’s Underground division.
Deep Automation includes:
- Deep Insights creates transparency through data in underground operations, enabling continuous improvements of an automated fleet.
- Deep Fleet Simulations for simulating a production area before developing the mine or implementing automation solutions.
- Deep Safety which provides flexible zones and access control to a production area, allowing for new vehicles to be checked in safely without interruptions.
- Deep Routes for recording, tuning and teaching routes to the smart machines.
- Deep Control for controlling safety, production assignments and autonomous traffic in real-time.
“With Deep Automation, we want to convey the qualities of our advanced yet easy-to-use automation solutions for material handling – with natural associations to operations deep underground, deep tech and our strong focus on deep partnerships,” says Sarah Hoffman, VP Sales & Marketing at Epiroc’s Underground division.
All trucks and loaders within Epiroc’s Smart and Green series – namely Scooptrams ST14 SG, ST18 SG, ST14, ST7 and ST18 S plus Minetruck MT42 are prepared for automation and remote control thanks to RCS - Rig Control System.